Do you work on a busy construction sites?
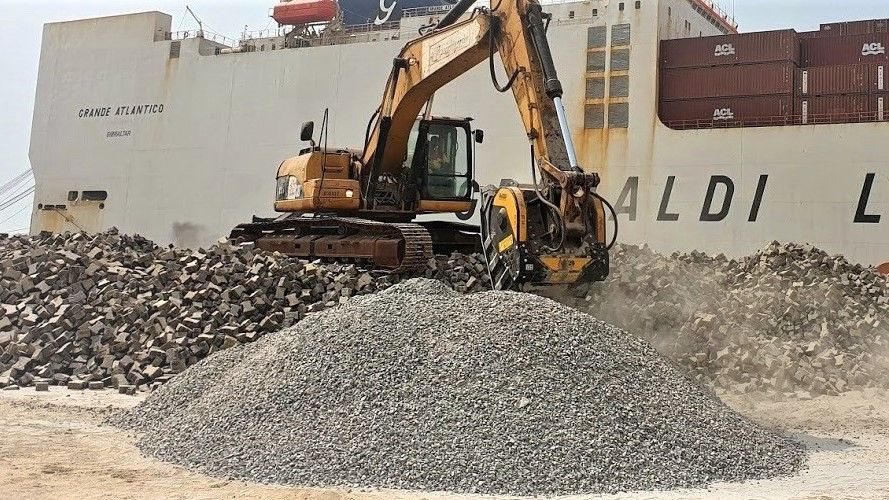
Demolishing, redeveloping, and building on ports and airports are jobs that have many constraints, and with there being a constant flow of arrivals and departures happening during the day and night, combined with the large quantities of waste material that need to be managed. This creates a logistical headache that can be solved if the job is done:
- Quickly
- On site
- Without extra costs
How can you accomplish this? With MB Crusher units, the problems surrounding busy construction sites are quickly resolved and companies that work on sites on seaports and airports improve their operations and profits.
HERE ARE SOME CONSTRUCTION SITES WHERE
MB CRUSHER MADE PROFITS TAKE OFF WHILE REDUCING COSTS
CRUSH INERT MATERIAL AND REDUCE TRANSPORTATION COSTS
Every year at the port of Conarky in Guinea, they record about 2 million tons of goods that arrive at the port. An investment of about 300 million dollars was meant to renovate the storage container’s deformed flooring that had warped due to storing heavy materials.
THE OBJECTIVE: To eliminate the current self-locking concrete blocks, reinforce the subsoil and lay down new concrete.
THE SOLUTION: MB’s BF80.3 jaw crusher. With this single unit installed on an excavator, the customer crushed the existing blocks on site, reducing them to an output size between 0-3 cm (1” minus). They then distributed the material over the substrate, creating an excellent mixture capable of withstanding heavy loads. This job was done with little maneuvering space, while eliminating the costs associated with material hauling and avoiding vehicles traveling to and from the job site.
REDUCE THE VOLUME OF DEBRIS WHILE AVOIDING HAULING SERVICES
In Tripoli, they needed to remove the debris from the collapsed buildings surrounding the airport, due to bombings. They needed to do this without hindering the airport’s operations. An airport in Hong Kong also faced similar issues when they needed to redevelop their infrastructure.
THE OBJECTIVE: clear the area quickly, avoiding increased vehicle traffic.
THE SOLUTION: in both situations, using the BF120.4 jaw crusher made it possible to reach every corner of the construction site, reducing the debris to their desired output size. The crushed material was used as a substrate on other job sites.
The convenience of directly recycling materials was that they eliminated the need to haul material from and back to the jobsite while eliminating the call for new material.
WORK IN LIMITED SPACE AND QUICKLY
In the seaport area at Dublin, Ireland, they needed to bring a crusher to the construction site only accessible through narrow and old alleyways.
THE OBJECTIVE: to reduce transportation costs and process material on location.
THE SOLUTION: The BF120.3 crusher bucket arrived on the construction site already installed on the excavator and traveled through the old and narrow alleys comfortably.
The crusher allowed the customer to immediately dispose and recover the debris, obtaining ready-to-use material that was used to construct a new 8 story complex. The recycled material that the crusher bucket produced has become a source of income.
PRECISION TO REDUCE WASTING RESOURCES
We traveled to Far East Japan at an important seaport. The job was to reinforce the existing storm surge barriers that protected the infrastructures surrounding the seaport.
THE OBJECTIVE: to grind the concrete surface in a space with limited maneuverability while generating as little waste as possible.
THE SOLUTION: Thanks to its precision, the MB-R800 drum cutter removed the concrete surface to ensure that the new casting adhered to the old surface. This secured a waterproof and stable structure, that could externally drain water, all without creating waste material.