Screening Bucket segregates GSB and input material for secondary crusher out of quarry's overburden
An established Black Rock quarry owner in the Eastern part of India was looking for a solution which would help them precisely segregate 60mm above material from the waste material derived from their blasting operations.
Solution was found by adding a Screening Bucket MB-S18 to their current fleet, as they needed an efficient, mobile, quick and cost efficient solution to use that material.
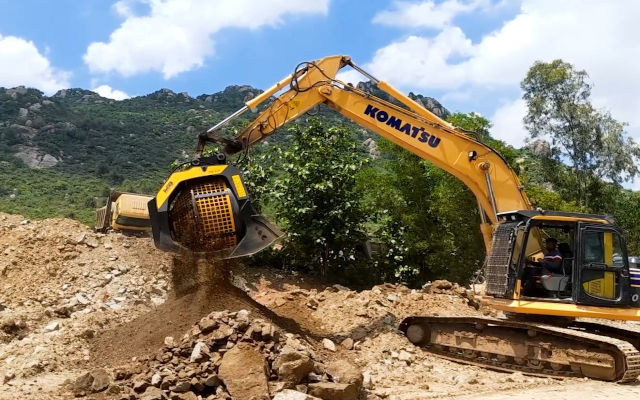
The blasting process left with a lot of wastage material to deal with
Customer was using blasting process for mining the black rock at site and using rock breaker to resize the material for primary crusher which eventually generates wastage material. Customer already owned a 220 TPH crusher.
Blasting and resizing of material for primary crusher generated a lot of wastage material which was a mixture of dust and soil up to 100 mm material. They had no use for that material, and previously they would create a pile of said material at site or sell it to other venders at a very low cost. Eventually they would just dump it in an unplanned manner, which was also a cost to them. All this process was time consuming and taking a lot of land within the mining area.
With the help of MB , the customer not only was able to convert waste material into useful material but was also able to generate a new income stream for their business
I need a Screener for my jobsite
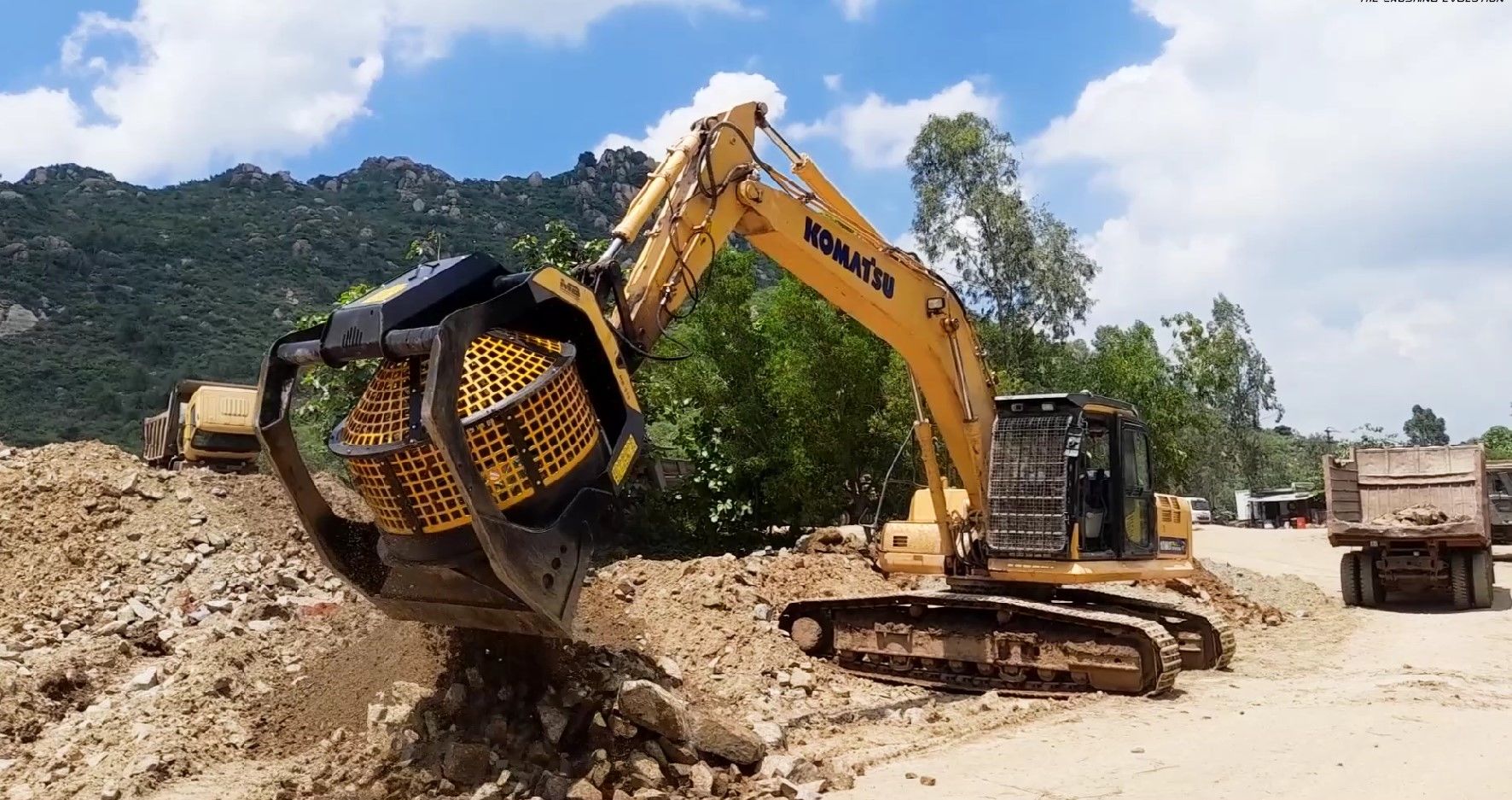
Screening Bucket was a game changer
By using the Screening Bucket MB-S18 mounted with 60X60 mesh, the customer is now segregating 60mm down material as GSB and sending 60mm above material for further processing to secondary crusher, which is increasing efficiency of crusher plant.
Furthermore, customer is able to now sell segregated GSB Material to road contractors which is, in turn, adding a new income source.
With one hour of operation with MB-S18 Screening Bucket the customer is able to get around 40m3 material as input for secondary crusher which has tremendously increased efficiency of existing crusher; while at the same time also getting 20m3 GSB Material that is being sold to road contractors.
This new income stream is generating an additional 50,000 to 60,000 Rs. daily.
The Screening Bucket MB-S18 has not only helped increase overall efficiency, but it has also enabled more profits and optimal utilization of resources.
I want to optimize my site
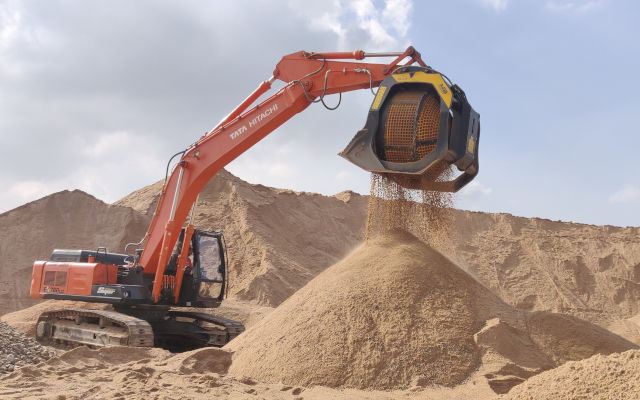
Focus on the Screening Bucket MB-S18
Applicable to any brand of excavator from 20 to 35 tons, it allows the selection of natural materials of several dimensions. The mesh is composed by interchangeable panels that allow a quick maintenance at site.
The MB-S screening bucket line allows to sift faster and better quality material, to finish the your job sooner, in half the time and to get ready-to-use material. Which means:
- reduced costs
- saving time
- increased profit margin
The use of a screening bucket before and even after the crushing phase can reduce your processing time by at least 60%.
After blasting the natural stones, the materials can be segregated to different sizes. The large ones can be sent to the crushing plant. The fine material can be precisely separated and re-sold as GSB.
All this with just the use of one operator + one excavator already at site, and in whichever point the material is placed.
The versatility of the screening bucket, attached to the excavator's boom, allows to segregate materials direcly on the truck as well, making them ready to be hauled away.
I would like to know the price