SAY GOODBYE TO TRAFFIC ON THE BV AUGUSTUS BRIDGE
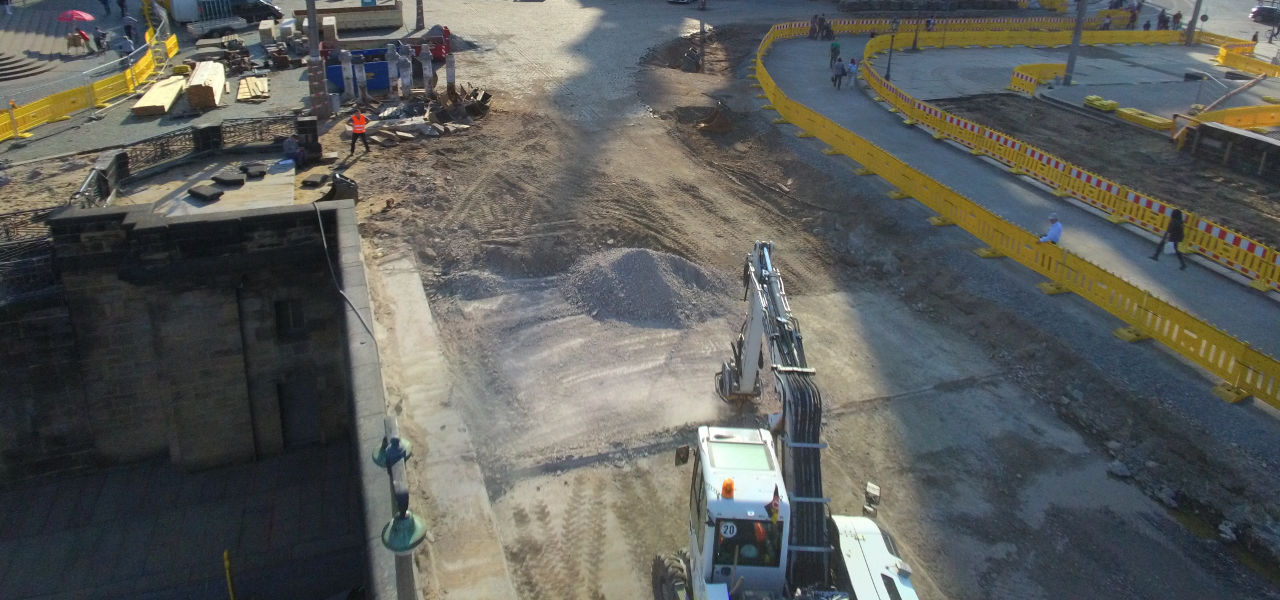
No cars will have access to the Augustus Bridge in Dresden until the end of 2019. Built during the 1700s, today the bridge is undergoing a complete restoration, which will return it to its original structure and repair the damages caused by the flooding of the Elbe in 2013.
Only some means of transport will be able to cross during the restoration: buses, taxis, rescue services, cyclists, pedestrians, and construction vehicles. And an MB Crusher milling machine.
That’s right, an MB-R800 (the milling machine for diggers from 10 - 22 tonnes) worked on the Augustus Bridge construction site for two months. Mounted on the digger Liebherr 918, the MB Crusher milling machine was used to destroy part of the cement that filled the bridge’s arches.
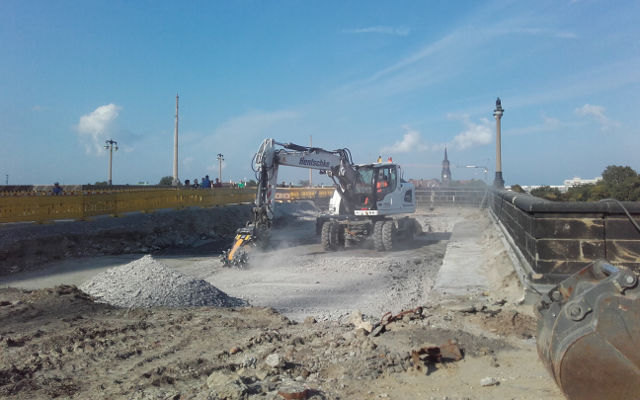
The historical bridge and the restoration works
The Augustusbrücke is 390 metres long and consists of nine arches. It connects the old district of Dresden with the new city, and it is one of the oldest junctions on the Elbe river. It is an historical bridge, for which 23 million Eurohas been allocated to the restoration fund. Once the restoration is done, passage over the bridge will be restricted to pedestrians only.
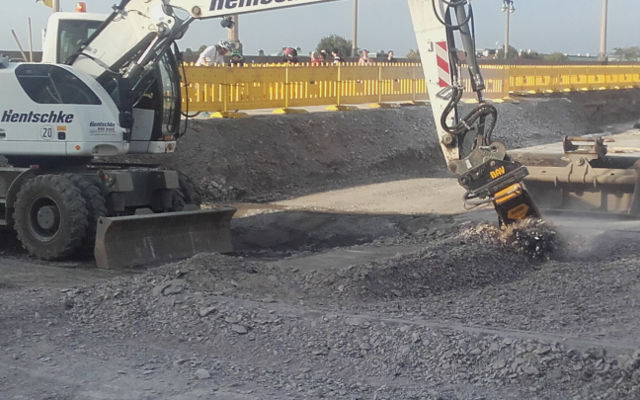
The MB Crusher Milling Machine at Work
The milling process was carried out in two stages. First, the MB milling machine worked on the bridge’s diagonal grout lines, to free the expansion joints. This was one of the most delicate phases, as it was necessary to work on it without damaging the structure. Then, the MB-R800 was used to remove part of the cement that filled the bridge’s arches, digging as far as 3 metres deep.
Once the milling work is finished, the arch will be filled with new cement and the walking area will be covered with the stones that previously formed the old structure. The bridge can therefore return to its former, original glory.
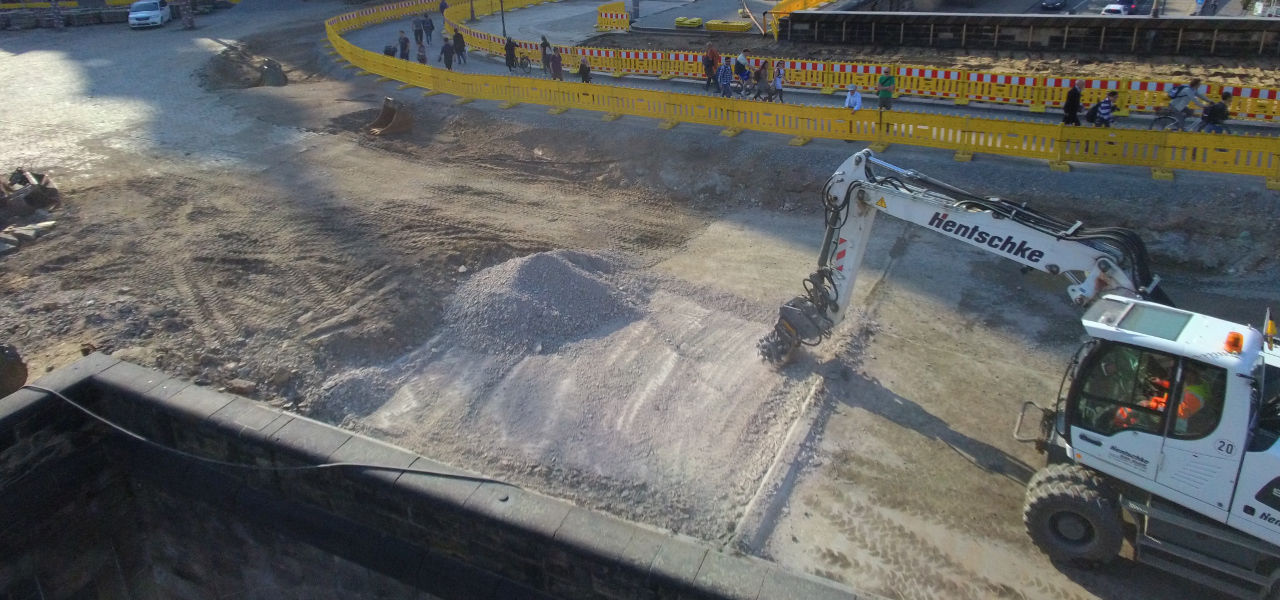
Focus on MB-R
There are three models in the MB-R range by MB Crusher: the smallest, the MB-R700, works with diggers from 6 to 13 tonnes; the MB-R800, the star of the Dresden construction site, weighs 1 tonne and adapts to diggers from 10 to 22 tonnes; finally, the largest in the series, the MB-R900, is for diggers ranging from 19 to 35 tonnes.
All models are equipped with an integrated safety system that intervenes if the digger's parameters are not properly adjusted. Not only that, the two drums can be dismantled directly on site, without having to take the milling machine to a specialised garage. On top of that, their uniqueness allows them to work even under water.
Even the digger is grateful when an MB milling machine is used. That’s right, because the milling machine uses a AAA+ hydraulic system with an integrated Power Booster which reduces the hydraulic power required by the operating machine. The direct drive twin motor system, on the other hand, is a patented system that allows the force of the two toothed heads to be distributed differently. This is a huge advantage, since the power of the two drums is managed according to the material's toughness and the vibrations sent through the digger’s arm are absorbed.
It is possible to work on different materials with the same milling machine, whether they are tough or less resistant: just choose between the low and full set of spikes to be used depending on the material to be milled.