MB Crusher’s smallest model gets an upgrade and wins the challenge against basalt
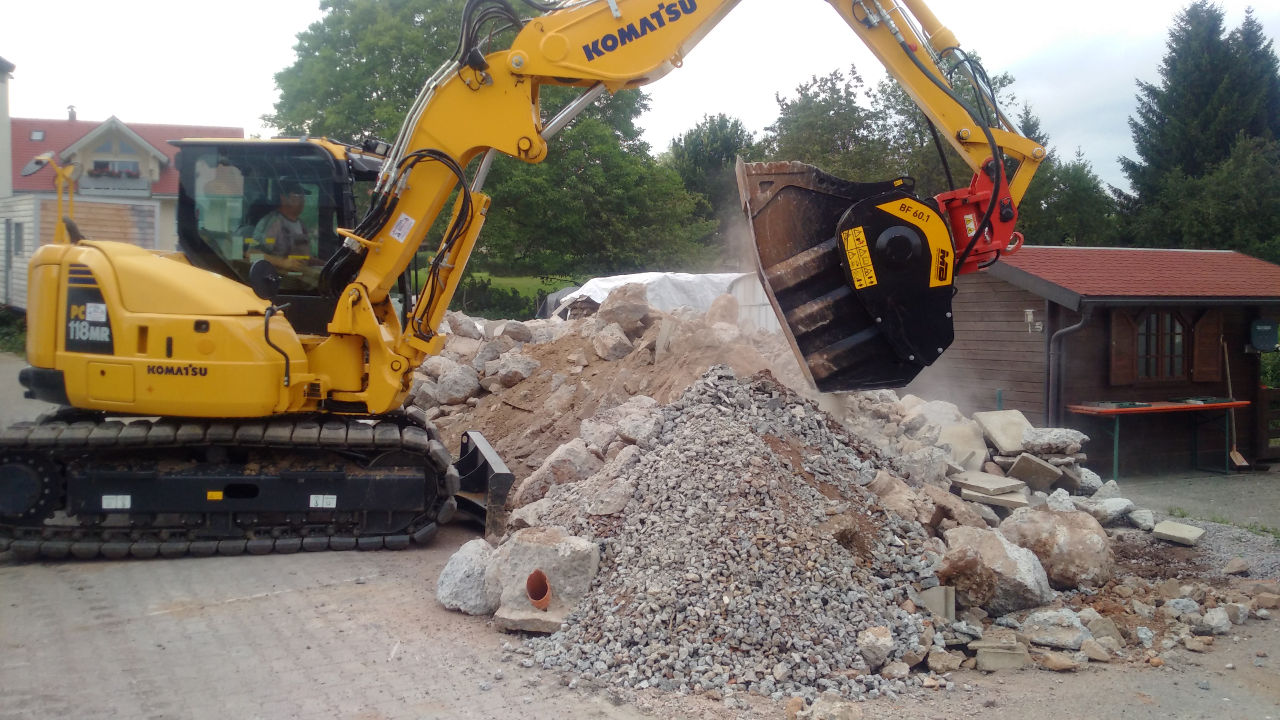
The theme of autonomy has always been a priority for many building companies. Being able to be independent in terms of fleet and operators allows for increased competitiveness in a sector in continuous evolution, that of recycling and construction. This means not having to hire equipment or depend on special skills brought in from outside the company, thus optimising costs and increasing competitiveness.
These are exactly the positive features underlined by the owner of the German company Schäuble Hoch- und Tiefbau GmbH in a recent interview. “After having purchased a BF60.1 crusher bucket in September 2016, something finally changed. I began to think freely about my business, free to programme my work and earn more.
“I was already aware of the advantages of MB in terms of cost reduction. Advantages resulting from the possibility to recycle materials on-site without having to dispose of them in a dump, with the opportunity of selling the same materials as new aggregates for the building industry,” stressed the company owner. “We mainly deal with materials from demolitions, which we then re-use for other kinds of work, such as filling excavations or for road beds. However, I would never have imagined that such a small bucket (the BF60.1) applied to my 12-ton Komatsu PC118 excavator would also allow for such highly efficient crushing of basalt. I am very satisfied with the reliability and productivity of this piece of equipment, just as I am satisfied with the after-sales service”.
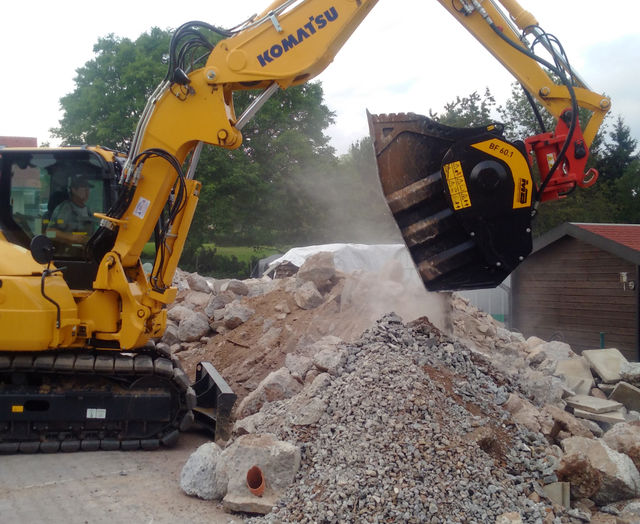
The evolution of the species: the new series 4 BF60.1
Suitable for heavy equipment from 8 tons upwards, MB's smallest model is now presented in the new S4 version: the fourth generation of crusher buckets. This is an updated and strengthened version, both in terms of structure and in a number of important technical details: first of all a restyling of the structural layout which allows for more agile movement and increased speed during crushing operations, facilitating its use on the excavator; the reinforcing of parts which are subject to particular stress, the new options for regulation, widening the range of the dimension of the crushed material, and lastly a new centralised greasing system that simplifies and speeds up on-site maintenance operations.
“A continuous challenge for improvement”, underlined Diego Azzolin, head of MB Crusher design and production, on presenting the latest innovations, “All our products undergo continuous testing and experimentation in order to improve them and render them more efficient in the various types of work sites that our clients deal with every day”.