Saving a week @ the time
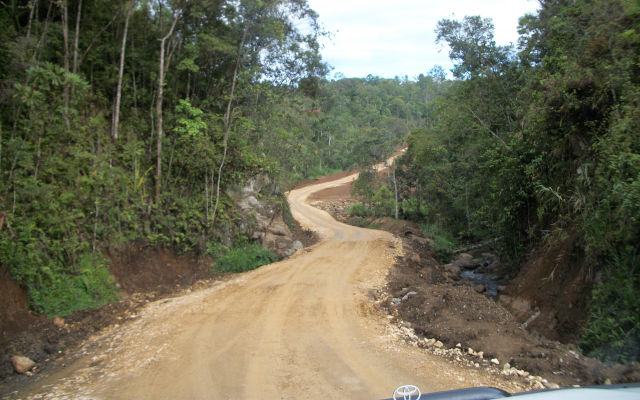
Working in the Pacific islands has its own unique challenges, obviously, there are many rewards as well; magical sceneries, mild climate, radiant turquoise water and gleaming shores. However, construction jobs in islands are usually complicated:
- Due to the lack of roads.
- Due to the condition of the road surface.
- Due to the size of existing roads.
- But mainly due to the absence of supplies.
Let just think of concrete, for example, in mainland there are selections of companies that will produce and supply it.
On an island, the market availability for materials is extremely limited, as they tend to have limited manufacturing capability, such as small factories that manufacture concrete blocks for example. Making construction jobs very challenging.
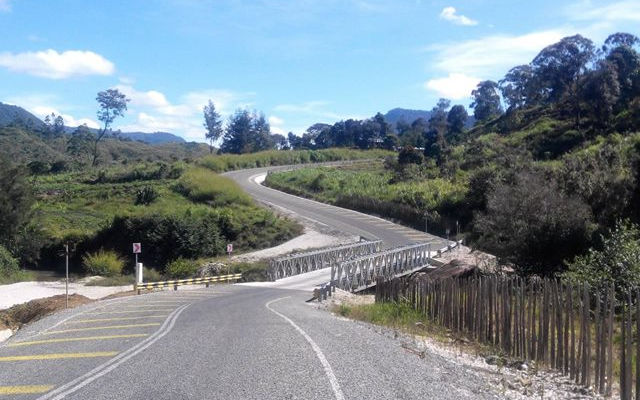
How to overcome this issue? With lots of ahead planning and time.
-
freight fees;
- import duties;
- schedule-slowing;
- wait for delivery periods;
- extra costs onto the project.
A better solution?
Let’s focus on what we don’t have and we need. And the solution is: to source locally using MB Crusher’s machines.
Steve West has taught us how he has done the job in Papua New Guinea, in the Pacific. He added to the fleet an MB Crusher screening bucket MB-S23 and began saving:
- Time, with MB’s screener the job is done in one day, saving a week processing time compared to the previous machine.
- Money, 200-300k’s on the cost of equipment purchasing.
- Energy, no power is needed to run the MB’S screener as the power source is the excavator.
The MB’s screening bucket took a week less to process the same amount of material than the screener they used before, and it is more cost-efficient in term of acquisition price and also in term of the running of the machine.
In fact, the MB’s screening bucket does not need extra power as it works with the excavator hydraulics. The efficiency of the screener is proven by the fact that in one day it sifts enough material for their need, ending up using the MB Crusher’s screening bucket every 10-14 days.