From one extreme to another: around the world touring the most spectacular construction sites
Rev your engines: to end the year on a high note, we’re taking you on a journey to see the most unique, extreme, and spectacular construction sites around the world.
From Tibet’s mountain ranges to Montana
- Difficulty transporting materials
- High costs
- Limited assistance
In Tibet, a company does road works and construction at 12467 feet above sea level, in a remote area surrounded by spectacular scenery. Using a BF70.2 crusher bucket, the company crushed waste on site and produced material to use as foundation of new construction projects. You obtain a big logistical and monetary advantage: with MB’s crusher bucket for excavators, you eliminate expenses when you purchase raw material for future projects.
While in Montana, the BF120.4 crusher bucket turned huge glacial erratics into aggregates that they can reuse on their job site. With the unit, they reduced their transportation expenses and gained new materials for future job sites.
From northern geysers to tropical seas
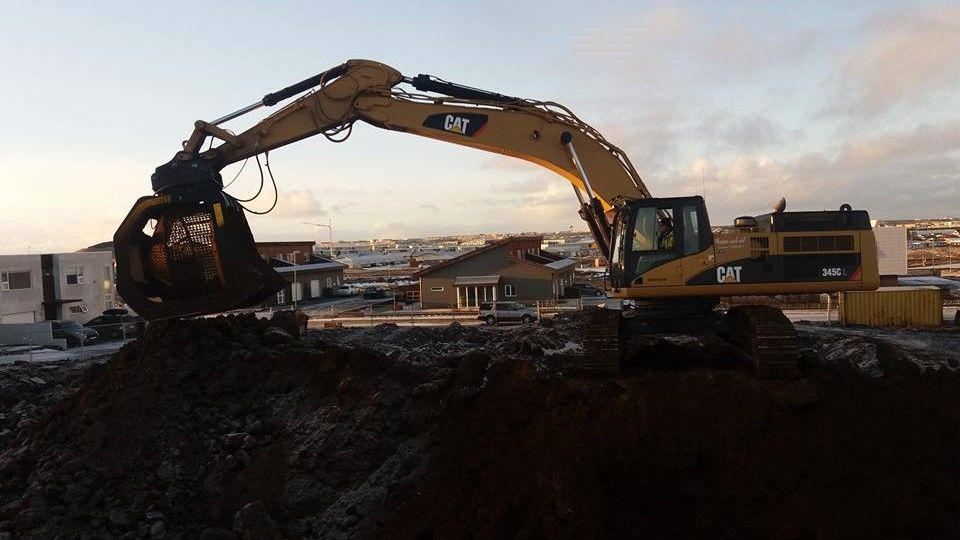
Some islands may be geographically far apart, but they share the same problems when it comes to construction sites:
- Transportation costs
- Difficulty obtaining materials
In Iceland, amidst spectacular landscapes dominated by volcanoes and geysers, an MB-S23 screening bucket installed on a Caterpillar 345C was the winning solution to select large quantities of basalt rocks and immediately obtain filler material to construct a hydroelectric power plant.
In St. Kitts and Nevis, a tropical island located in the Lesser Antilles, two MB Crusher units are working on a major redevelopment project
that involves renovating old colonial buildings and rearranging the natural landscape. Installed on a Caterpillar 320L, the MB-S18 screening bucket separates topsoil from leaves and brushwood, and the material is reused on site to beautify green areas. The BF90.3 crusher bucket is used to crush the local stone, a hard type of volcanic granite, the Nevis Stone.
Once crushed, the stone is reused to fill the holes that the excavations created that’s necessary to construct the buildings and create a new base for the local road network.
From the cold to the heat
Let's continue our journey to locations where temperatures reach extreme levels, affecting work on the construction site. These locations are characterised by several issues including:
- Finding equipment that can work in extreme weather conditions
- Logistical difficulties due to the nature of the locations
- A hard time finding materials
We are in Siberia where there’s an expanse of snow as far as the eye can see. Thermometers read -58°F during the day, roads that are almost empty, and you have mountains and forests to cross. Thanks to MB Crusher, a local company brought their BF70.2 crusher bucket to the quarry without struggling to transport it since it was mounted directly on the excavator. The crusher and the MB-S18 screening bucket to recycle the aggregates and reduce its size and reuse them to maintain the roads inside the quarry.
Something similar happened in Saudi Arabia with its 122°F summer temperature and its mountainous and desert terrain, where a BF90.3 crusher bucket worked in the most difficult of places inside a quarry and therefore not accessible by traditional means.
Finally, let’s do some wine tasting
Let's end our tour in Italy and France, countries known for an excellent product: wine. But what happens at the end of the season, when the only part of the vineyards remaining are the concrete poles are left? In this context, MB Crusher’s equipment proves to be an excellent ally, because it helps dispose of the material.
- Thanks to MB’s jaw crushers, you can recover concrete (and create a separate pile for the iron) quickly and without spending money on disposal costs.
- By installing a crusher on their excavator, the reinforced concrete poles can be crushed while the iron comes out of the unit’s mouth.
- If iron needs to be separated, it’s possible to use an iron separator, an accessory compatible with some crusher bucket units and is conveniently operator from the cab.
The unit is a big time-saver, which translates into economic and environmental benefits.